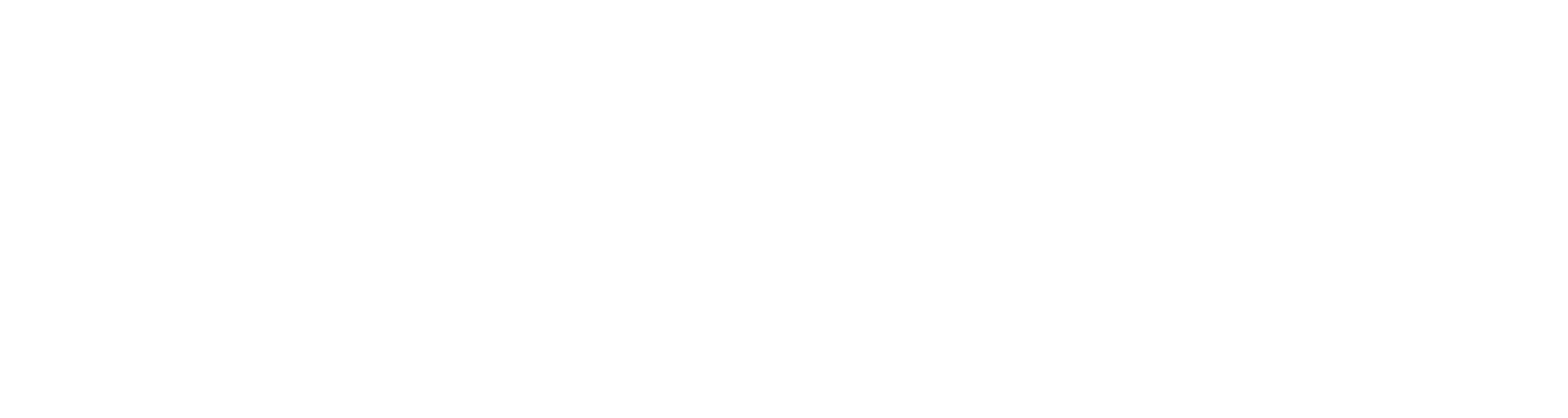
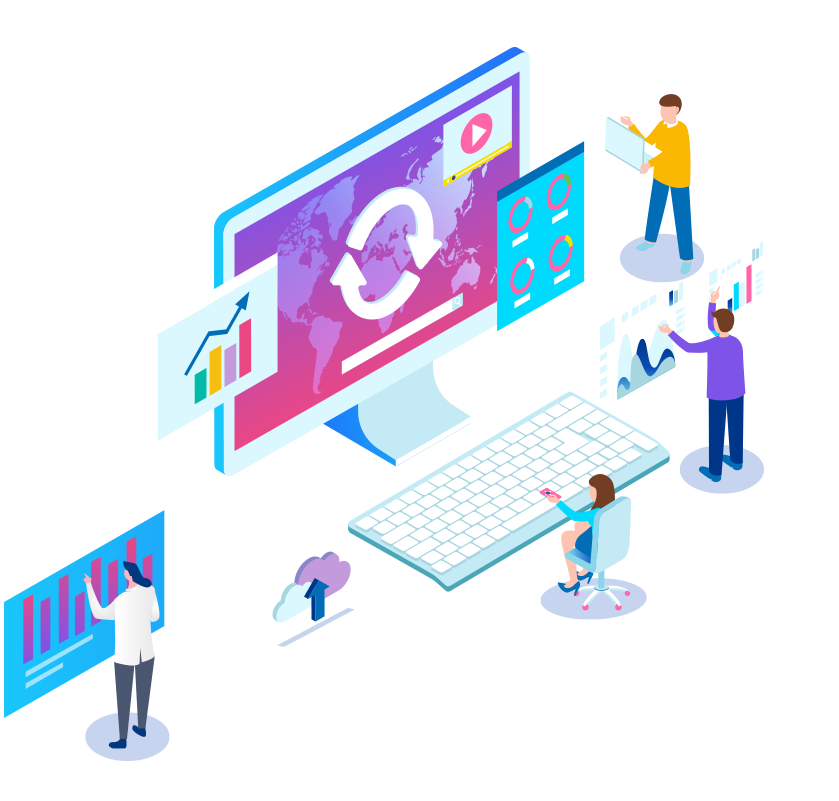
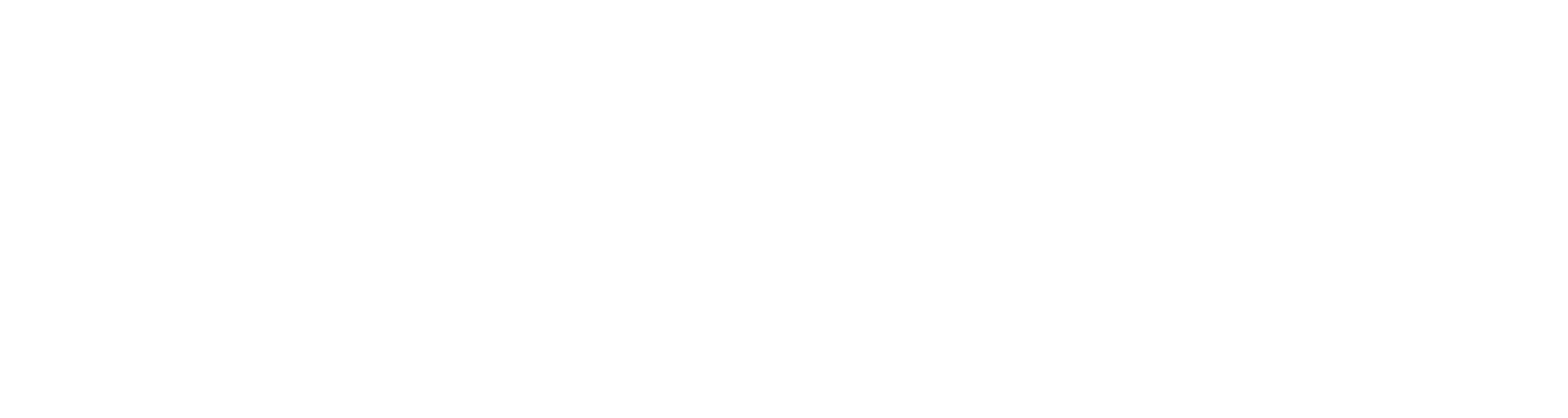
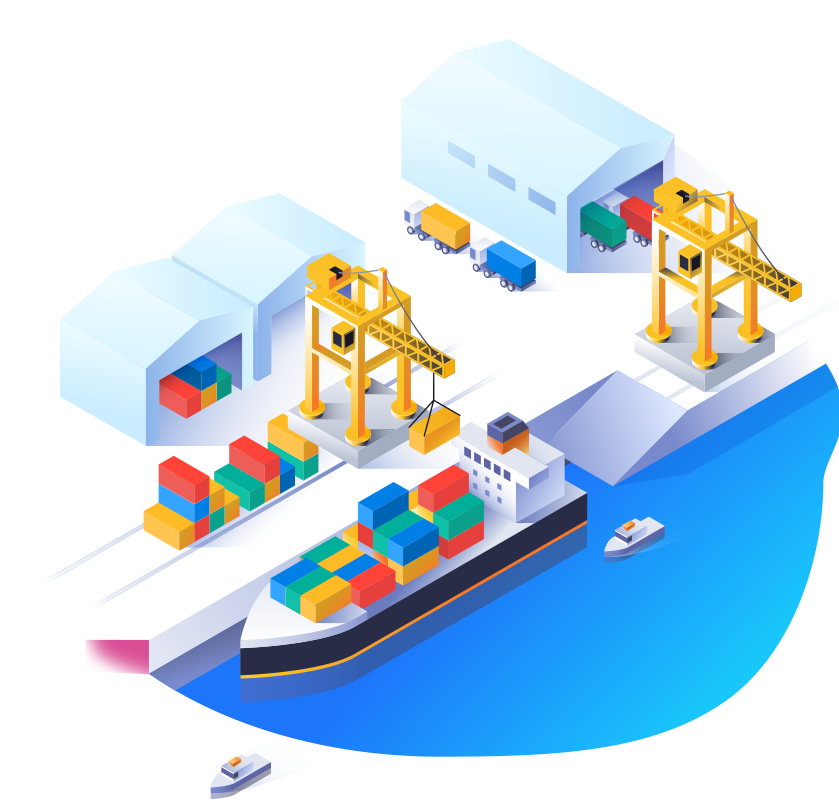
題解決を、最高のプロがサポートします。
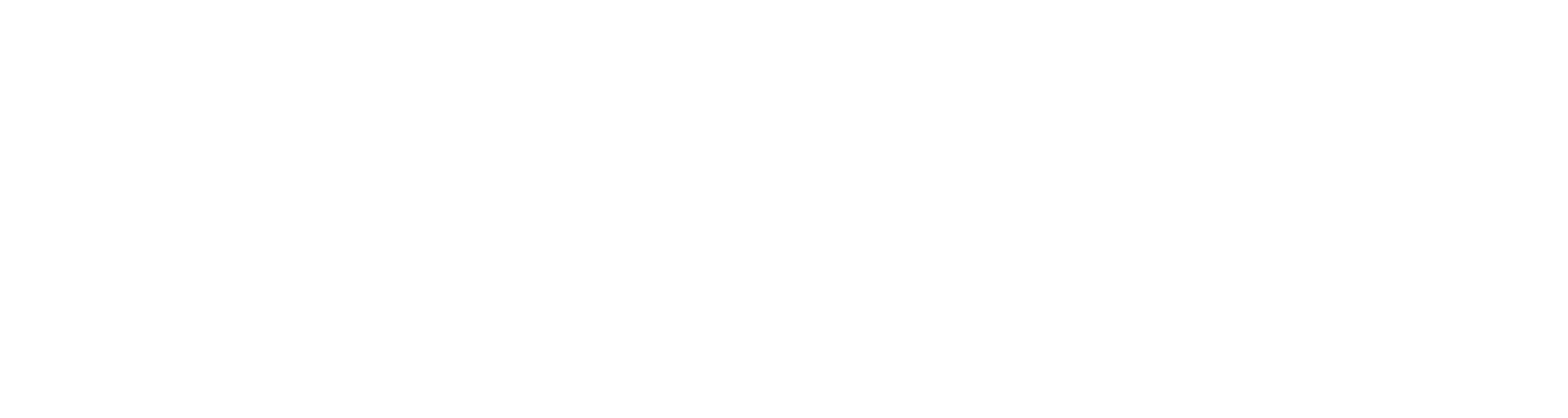
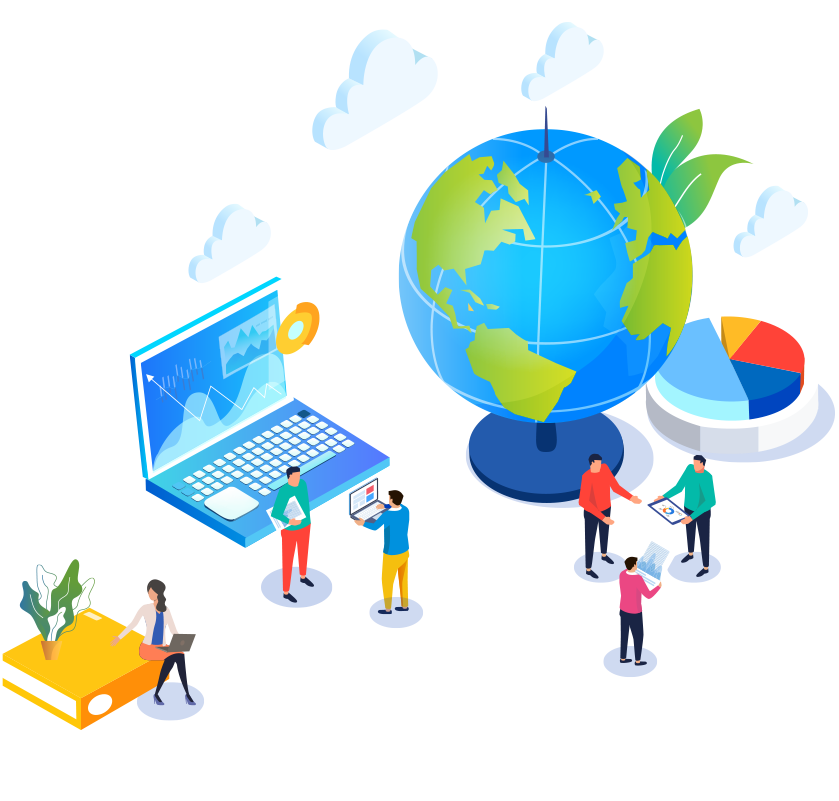
社会的責任を果たし、持続可能な発展を実現しながら、
ステークホルダーの皆様からのご意見に耳を傾けます。
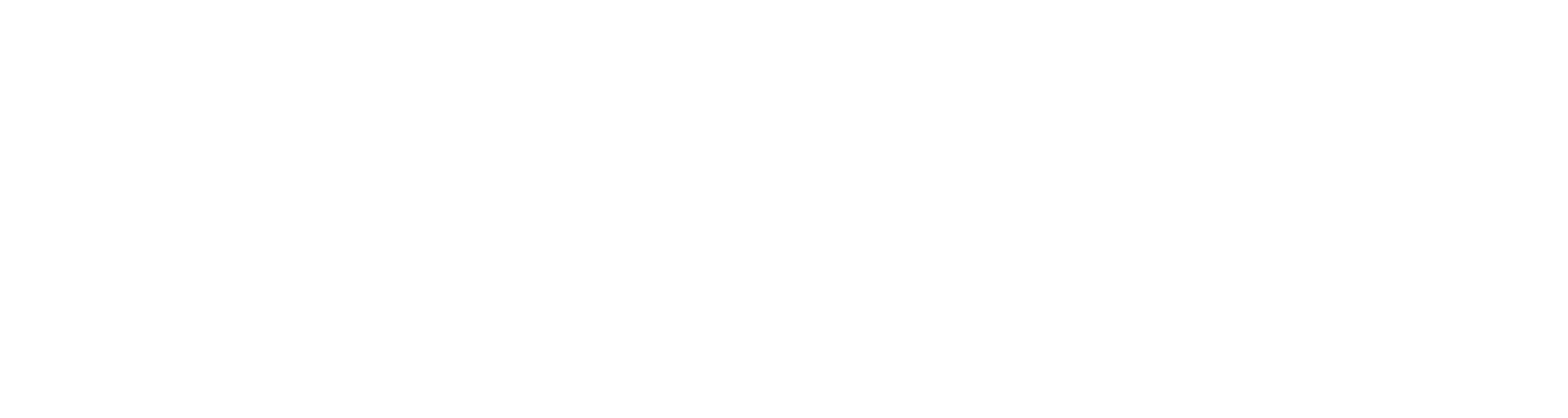
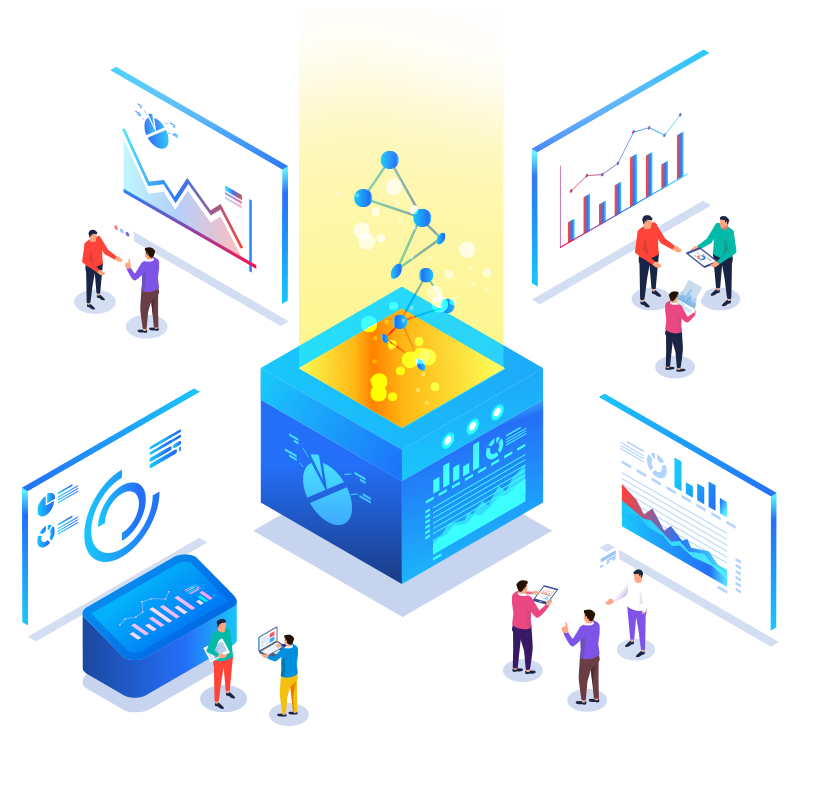
About CLT
サイバーロジテックは革新技術に基づき、グローバル物流産業界へデジタル・トランスフォーメーションを提供しております海運、港湾、物流専門IT企業です。
20年超え多くの船社、ターミナル、物流企業のパートナーとして経営活動を最適化し、先端プロセスによる統合プラットフォームを提供してきました。
我々はお客様の業務効率化、競争力強化、生産性やサービス品質を向上させる為に、業務自動化、コミュニケーション、協業が改善できるツール、ソリューション開発に最善を尽くしております。
-
22+ Years
-
700+ Employees
-
15+ Shipping Companies
-
36+ Terminals
-
140+ Logistics Companies
-
30+ Countries

SOLUTION INFORMATION
サイバーロジテックは物流産業はもちろんのこと、海運・港湾産業界の先導者として革新技術をもとに、グローバルサプライチェーンにおける課題を解決し、
可視化を実現する等、急変するマーケットのニーズに迅速対応できるコンサルティングサービスや産業全般にわたってスムーズに拡張可能のソリューションを提供しております。
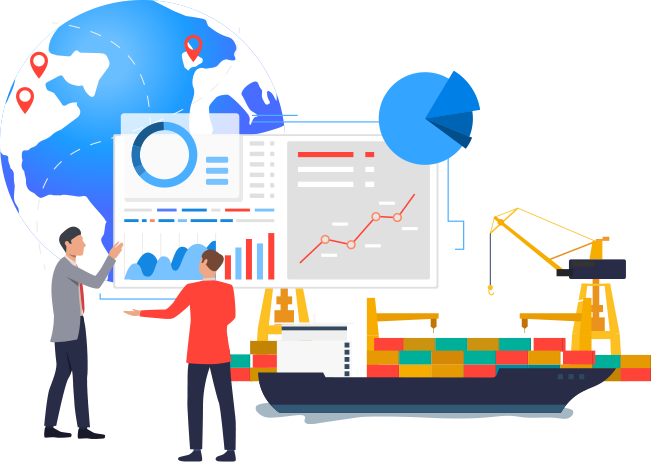
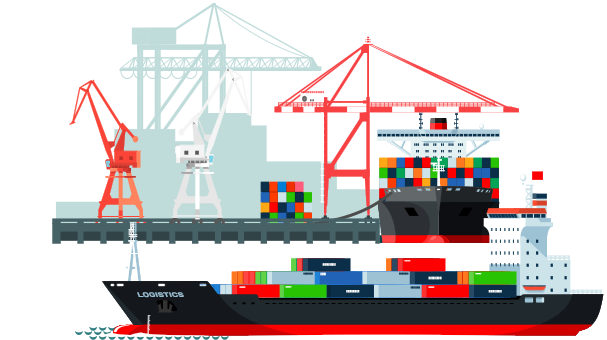
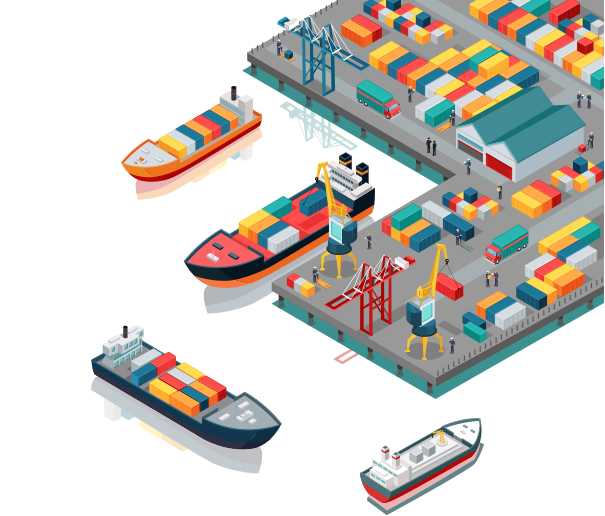
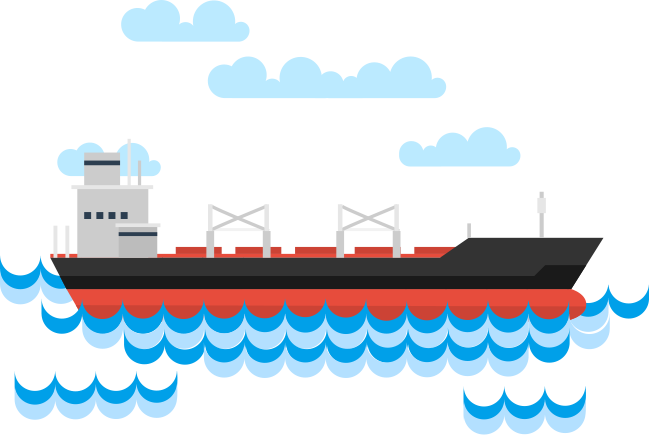
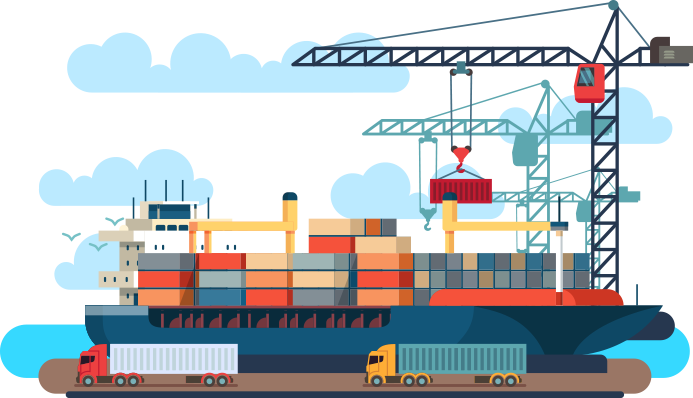
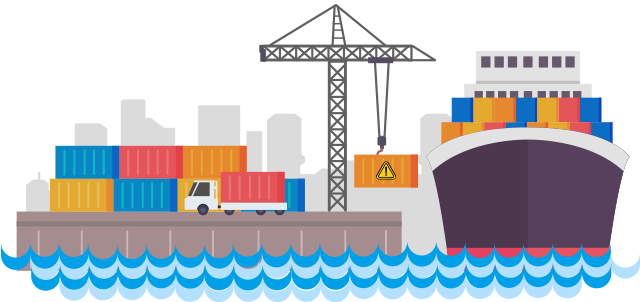
- ALLEGRO
-
Container Shipping Liner Solution
ALLEGRO は海運船社のサービス競争力向上やダイナミックなグローバル環境変化に対応するために、先端の運営システムとプロセスを導入するなど、デジタルトランスフォーメーション(DX)を支援する、船社向けのソリューションです。 ALLEGROはウェブベースの オープン アーキテクチャでカスタマイズの安定性を保障し、またグローバル船社による検証済みの、統合運営ソリューションです。
- OPUS CONTAINER
-
Container Liner Operation Solution
OPUS Containerはコンテナ・オペレーションに関する 全てのビジネスの効果的統合管理ができるコンテナ 海運向けのソリューションです。船積み依頼から目的地へ着くまでの全行程につき、国際標準に則った手続きを採用し、プロセスの集約的、体系的な管理が可能です。
データごとの分析レポートを活用することで、ビジネス経営における可視性を向上し、採算性重視の経営に貢献できます。
- CARA
-
Carriers Collaboration Solution
CARAは複数の船社同士とのコミュニケーションや 協業の強化を目的として立ち上げた統合プラットフォームです。世の中で自社、独自のトン数、スペースを保有、使用している船社は存在しません。すべての船社は他社と組んで、スペースを借り貸し、売買、交換したり、共同運航やアライアンスを構築したりしています。
- OPUS Bulk
-
Bulk Shipping Solution
OPUS Bulkは、大型および中小型のバルク船社における戦略的意思決定を支援し、事業実績を分析する為のバルク輸送事業向けのソリューションです。頻繁に急変するバルク輸送マーケットに対応するため、バルク船社はDXを進め、一層、効率よく、業務プロセスを管理し、データを分析することで運営効率性を図るべきです。
- OPUS Stowage
-
Stowage Planning Solution
Opus Stowageは、コンテナ船社のコンテナ輸送を効率よく行うため、最適の本船積み付け計画を提供するソリューションとして、ターミナルと組んで船積み作業を要請するなど、一連の積み付けデータを管理します。
- OPUS DGL
-
Dangerous Goods Management Solution
今まで海運業界では、海上輸送中に起こりうる危険事故を事前に予防する為、特殊貨物の中でも危険物の管理が最も重要な懸念点でした。しかし、近日は海上輸送の急増により、特殊貨物も増加し、より安全で、体系的な危険物管理が一層重要な課題として認識されております。OPUS DGLは、海上輸送のため積まれた特殊貨物の中でも危険物へフォーカスしている危険物向けの統合管理ソリューションです。
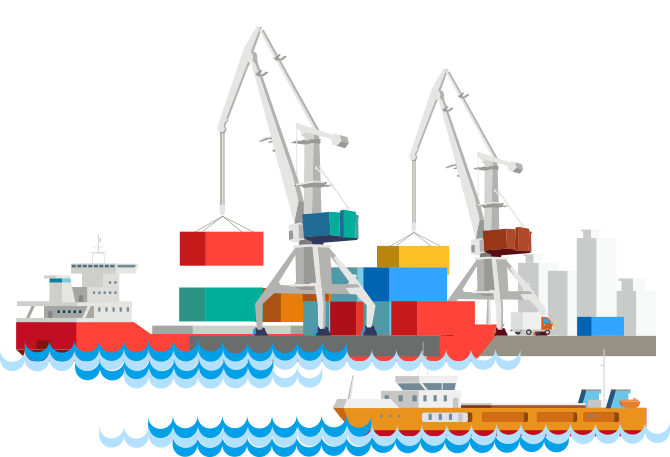
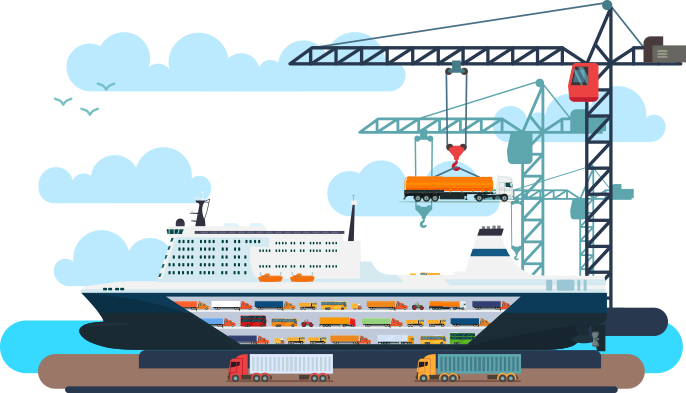
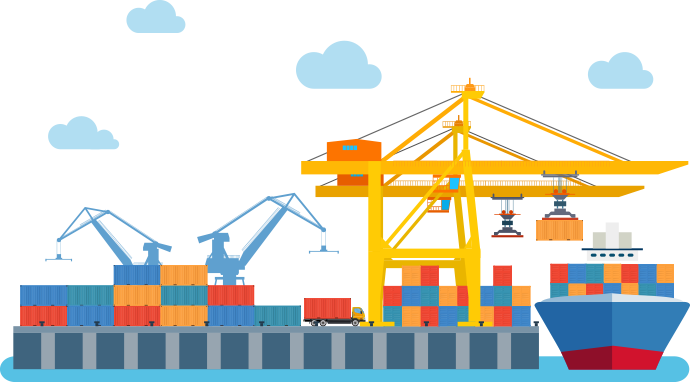
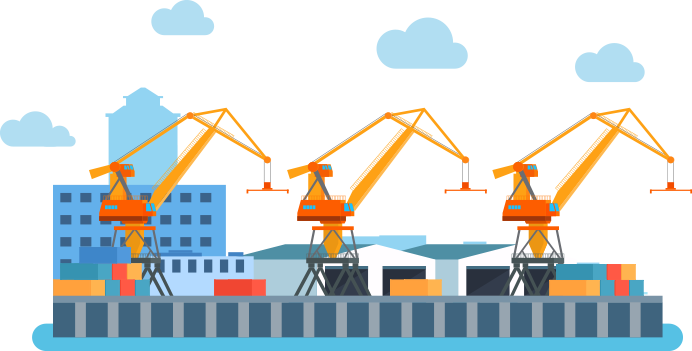
- OPUS Terminal
-
Container Terminal Operation and Decision Support System
OPUS Terminalは、コンテナターミナルなりではのタスクであるコンテナの船積み/陸揚げ、仕分け、保管はもちろん、新たに必要となるターミナル業務にも柔軟に対応できるソリューションです。 海上貨物の輸送量は年々増加を続けており、海運業者はアライアンスの強化や船舶の大型化などにより物量増加に対応しています。
- OPUS Terminal M
-
Multipurpose Terminal Operation System
OPUS Terminal Mは、コンテナ貨物、一般貨物、RORO貨物などのオペレーションを支援する、多目的ターミナル向けソリューションです。コンテナ、RORO、ばら積みターミナルでも、多様な貨物を処理する多目的ターミナルでも、1つのシステムであらゆる貨物を扱うことができます。
- OPUS DIGIPORT (EAGLE EYE)
-
Digital Twin and Data Analysis Platform
現在、多くのターミナルでは、効果的運営や安全を目的として、ターミナルオペレーティングシステム(TOS)やゲート、港内外トラック、クレーンに至るまで様々なターミナル装備・機器を有機的連携、相好運営の実現を目指しています。OPUS DigiPortは、IoTプラットフォームに基づく2D/3D仮想ターミナルシステムです。
- TABS
-
Total Advanced Billing System
TABSは複雑なターミナル請求業務を自動化し、お客様に24時間オンラインサービスを提供する、ターミナル向けの自動請求業務システムです。世界中のターミナルは半自動から完全自動化に発展し続けています。しかし、ターミナル業務のうち、料金計算を含む請求業務だけは、自動化されにくく、ややこしい作業ともいえます。ターミナルの料金はサービスや顧客ごとにかなり複雑であり、タリフさえもその体系が異なります。
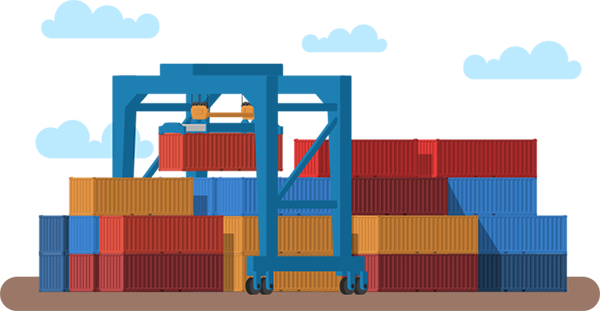
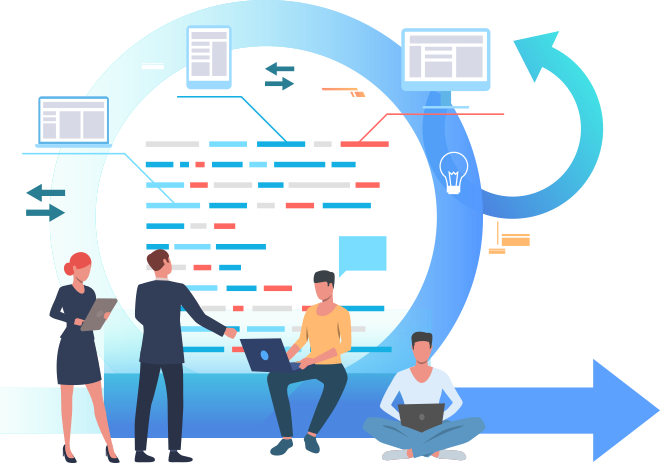
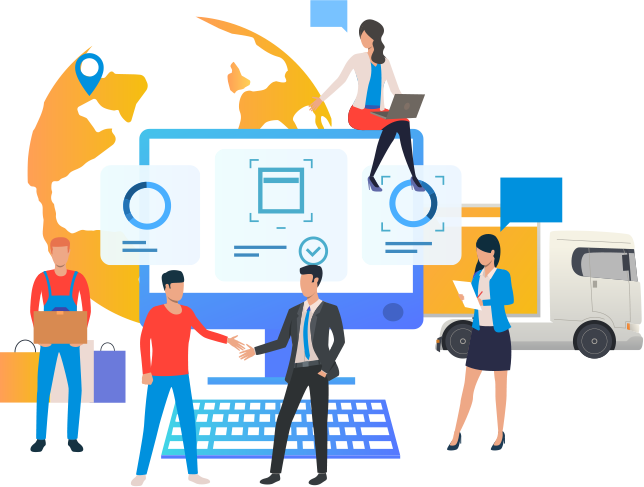
- OPUS D&D
-
Demurrage & Detention Management Solution (SaaS)
OPUS D&Dは、船会社/国別の祝日および週末情報とタリフ情報に基づいて、複雑な手作業の代わりにデマレージとディテンション費用を自動的に計算してくれるソリューションです。 過去数年間、フリータイムは短くなる一方、デマレージとディテンション料金は世界的に引き上げられるにつれ、デマレージとディテンションのコスト削減が運送業者の主要課題として浮上しました。
- SMARTLINK
-
Data Integration Platform
SmartLinkは、データやテクノロジーを活かし、物流を繋ぐB2B iPaaS型のプラットフォームです。グローバル船社のEDIサービスをはじめ、フォーワーダーのニーズに応じ、米国政府による出港前報告精度(AFR)向けの機能を開発、提供開始することで、SmartLinkの歴史が始まりました。続いて、米国以外、他国の税関申告、船社・荷主のデータ連携、物流業向けのEDIサービス等、少しずつビジネスモデルを増やし、サービスを展開してきました。
- CARIS
-
Freight Forwarding & Warehousing Solution
現在、フォワーダーを始めとする物流関係者にとって、ビジネスプロセスの柔軟性、輸送状況の可視化、コスト削減は非常に重要な課題です。CARISは、運送会社、NVOCCおよび3PLの貨物運送、倉庫管理およびグローバルネットワークの構築を支援するウェブベースの単一プラットフォームです。
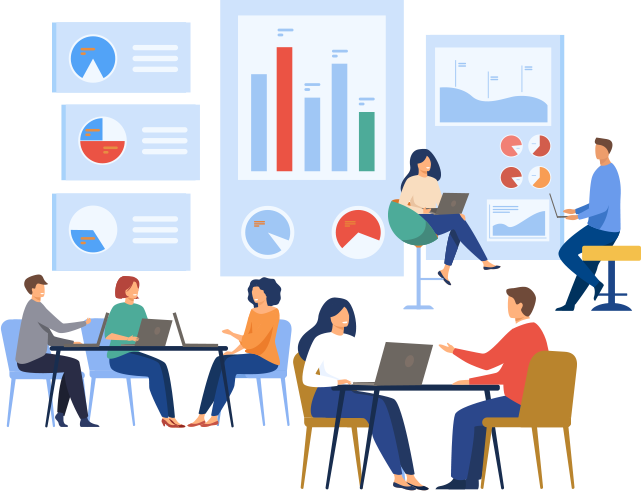
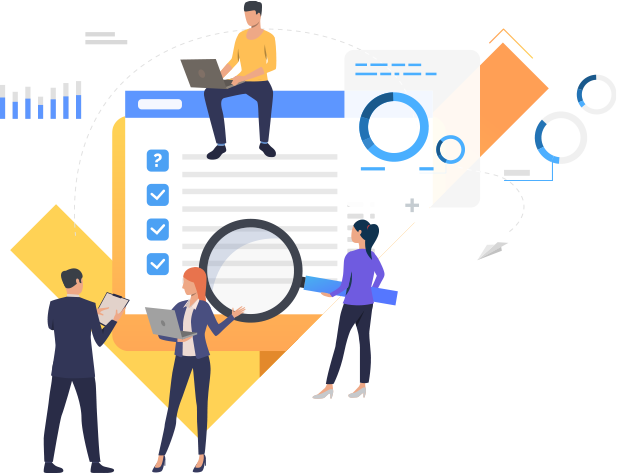
- ODC
-
Offshore Development Service
AI、IoT、メタバース等の普及やオンライン中心のサービスが急激に流行ることにより、法人向けのソフトウェア開発リソースの需要は伸び続いてますが、リソースは限られているため、希望リソースの適期採用は厳しく、人件費の急騰によって、法人としての負担も大きくなりました。サイバーロジテック提供のODCサービスとは、競争力のあるベトナムIT人員を活用し、様々な業界の法人様を対象として、ソフトウェアを開発、メンテナンス、及び、オペレーター業務を代行したり、支援するサービスです。
- SHINE
-
Positive Outcomes for Logistics Operations
産業構造の変化に伴い、自動化・データ化が進まれている最中ですが、産業プロセスの中では未だに手書きが多く、定型化されていないバラバラの書類作業が継続しております。SHINEは、発注や製造、調達、流通、消費者による購買、サービスの提供に至って、すべての商流、工程の中で発生する様々な形の文書を精度高く、迅速にデータ化し、管理するソリューションです。
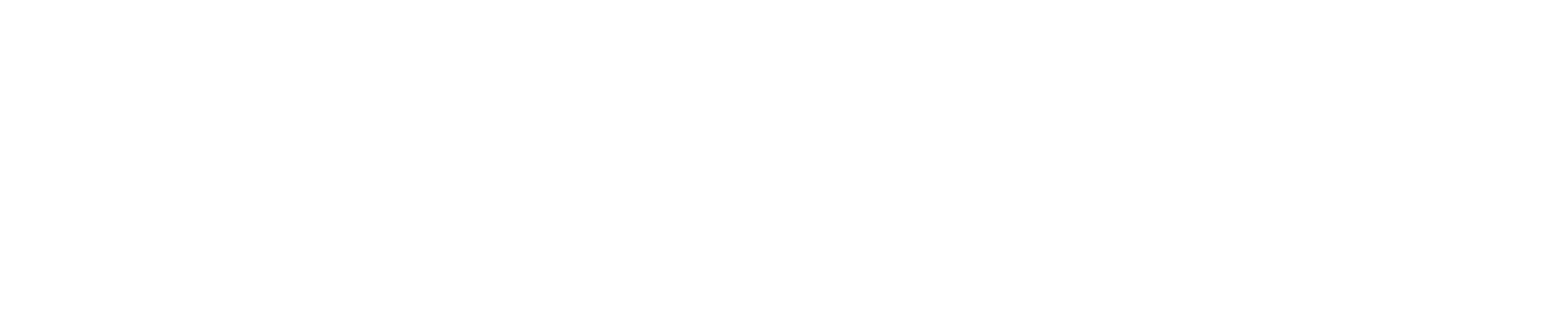
-
MAKING
THE WORLD’S TIME
AND SPACE
MORE VALUABLE - 世界の「時間」と「空間」の価値を高めていきます。
